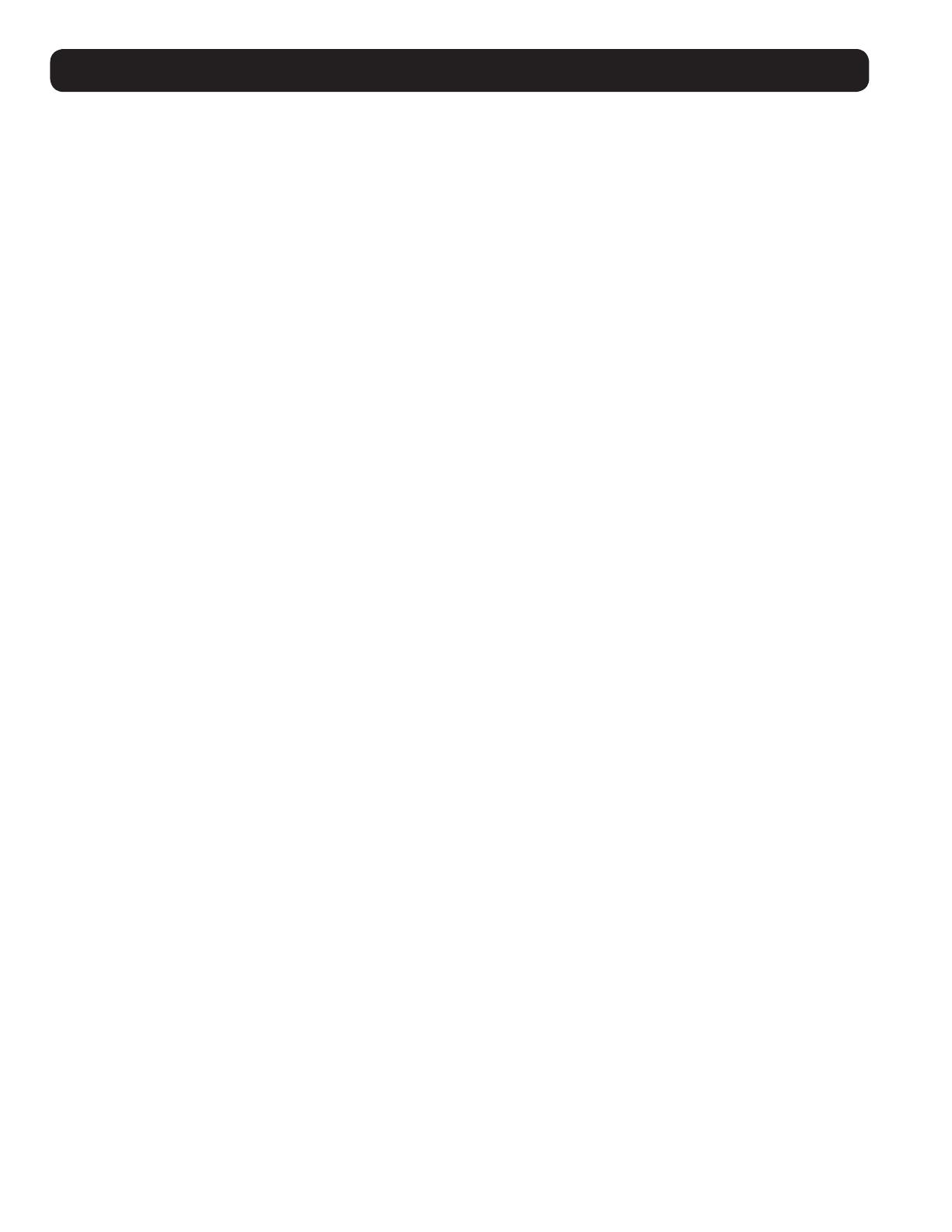
2
1. Important Safety Instructions ..............3
1.1 Placement Warnings ........................................ 3
1.2 Connection Warnings ....................................... 3
1.3 Usage Warnings .............................................. 3
2. Introduction ..........................................4
2.1 Product Introduction ........................................ 4
2.2 Functions and Features .................................... 4
2.3 Packing List .................................................... 5
2.4 Appearance .................................................... 6
2.5 Component Identification ................................. 6
2.6 Piping System ................................................. 8
2.7 Control Panel .................................................. 8
2.8 Network Interface ............................................ 9
3. Installation .........................................10
3.1 Installation Site ............................................. 10
3.2 Placement .................................................... 10
3.3 Handling ...................................................... 11
3.4 Positioning.................................................... 11
3.5 Side Panel Removal....................................... 13
3.6 Drilling Holes ................................................ 14
3.7 External Piping .............................................. 15
3.8 Power Connection ......................................... 16
3.8.1 Power ............................................... 16
3.8.2 Condensed Water Pipe ....................... 19
3.8.3 Control Box ....................................... 19
4. Initial Startup .....................................20
4.1 Pre-Startup Inspection ................................... 20
4.2 Power Supply ................................................ 20
4.3 Coolant Line Purge ........................................ 21
4.4 Operating Temperature and Humidity ............... 22
4.5 Water Leakage Detector ................................. 23
4.6 Water Balance .............................................. 23
4.7 PID Setting ................................................... 24
Table of Contents
5. Operation ............................................26
5.1 LCD Hierarchy ............................................... 26
5.2 Control Panel Operation ................................. 27
5.3 Status Screen and Main Menu ....................... 27
5.4 Account Authority and Login ........................... 28
5.5 Operation Modes .......................................... 28
5.6 Shutdown ..................................................... 29
5.7 Cooling Unit Settings ..................................... 29
5.7.1 Set Point........................................... 29
5.7.2 Local Setting ..................................... 29
5.7.3 Controller Setting ............................... 31
5.7.4 Alarm Setting ................................... 31
5.7.5 View System Status ........................... 32
5.7.6 View / Reset Running Hours ................ 33
5.7.7 View / Clear Event Log ........................ 33
5.7.8 Changing System Type ....................... 33
5.7.9 Restoring Default Settings .................. 34
5.7.10 Setting Automatic Control Mode .......... 34
6. Network Configuration ........................ 35
6.1 SNMP Configuration ...................................... 35
6.1.1 Configuring via Web-Based Interface .... 36
6.1.2 Configuring with TLNET (System) .......... 37
Configurator
6.1.3 Configuring via Telnet ......................... 38
6.1.4 Configuring through COM Port ............. 39
6.1.5 Configuring via Text Mode ................... 40
7. Precision Cooling Dashboard
Software .............................................43
7.1 Monitor ....................................................... 43
7.1.1 Status and Information ....................... 43
7.1.2 History .............................................. 44
7.2 System ....................................................... 45
7.2.1 Administration ................................... 45
7.2.2 Notification ....................................... 49
8. Optional Accessories ..........................52
9. Maintenance and Cleaning .................52
9.1 Firmware Upgrade ......................................... 52
9.2 Storage ........................................................ 52
10: Troubleshooting ................................ 53
Appendix 1: Technical Specifications ......56
Appendix 2: Periodic Inspection / .......... 57
Maintenance List
Appendix 3: Glycol Correction Table .......59
Appendix 4: Warranty and ......................59
Product Registration