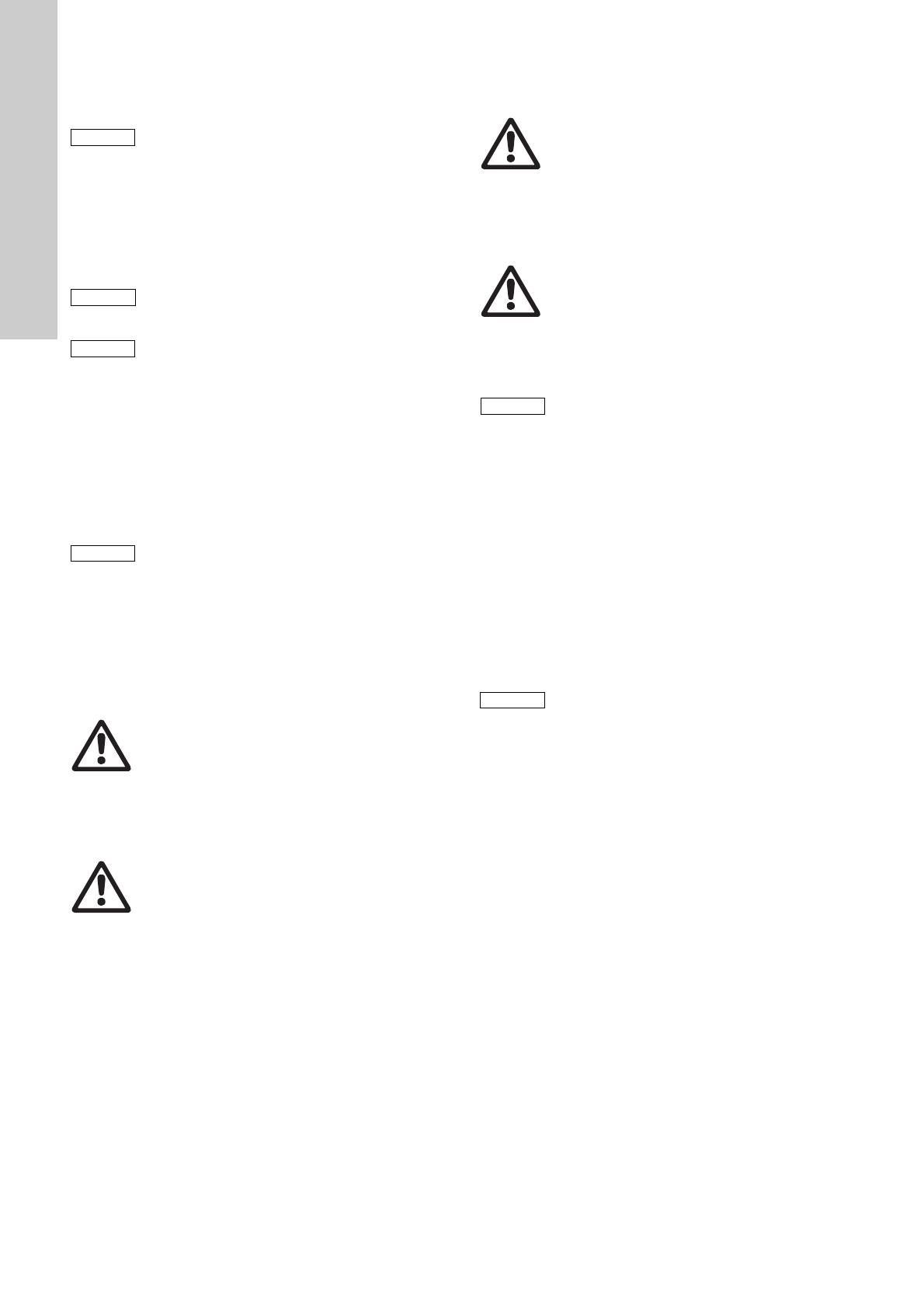
English (GB)
12
5. Commissioning
5.1 Transport and storage
5.1.1 Unpacking
• Check the DTS dosing tank station for visible transport
damage immediately after receipt.
• Dispose of the packaging in accordance with local regulations.
5.2 Installation
5.2.1 Installation site
The installation site must be horizontal, even, frost-free and
suitable for the corresponding loads.
The DTS dosing tank station must be easily accessible.
Avoid direct sunlight. The materials of the DTS dosing tank
station may be damaged by sunlight.
When installing the DTS dosing tank station outdoors, provide
protection from rain and weathering.
5.2.2 Hydraulic connection
Depending on the scope of supply, the customer must install the
components.
Refer to the installation and operating instructions for the
components used.
5.2.3 Installation of the dosing pump
• Mount the dosing pump with the suitable installation material
directly on the dosing tank or adapter plate.
Refer to the installation and operating instructions for the dosing
pump.
5.2.4 Installation of the multi-function valve
• Fit the multi-function valve directly on the pressure valve of the
dosing pump.
Refer to the installation and operating instructions for the multi-
function valve.
5.2.5 Installation of the dosing lines
Connect the suction line to the suction valve of the dosing pump.
Connect the discharge line to the discharge valve or to the multi-
function valve of the dosing pump.
1. Cut the hose ends to length (straight cut).
2. Pull the union nut and the clamp ring over the hose.
3. Slide the hose end over the connector until the stop, widen if
necessary. Depending on the type of connection, secure it
with a counterpiece or a hose clip.
4. Fit gasket.
– Ensure that the O-ring or flat gasket is positioned correctly
in the counterpiece (pump valve/injection unit).
5. Use the union nut to screw the hose on the valve.
Refer to the installation and operating instructions for the dosing
pump.
5.2.6 Installation of the injection unit
• Screw the injection unit into the coupling thread (provided by
the customer) of the process line vertically from above.
Refer to the installation and operating instructions for the injection
unit.
Do not throw or drop the DTS dosing tank station.
Only transport the DTS dosing tank station, if the
dosing pump is disassembled.
The DTS dosing tank station may contain water from
the check carried out in the factory.
Some media react with water.
If you dose a medium that reacts with water, remove
the water from the DTS dosing tank station first.
Before starting work, check if all technical conditions
required at the installation site comply with the data
on the nameplate of the DTS dosing tank station.
Warning
The dosing medium is pressurised and can be
harmful. Observe the maximum permissible
pressure.
When working with chemicals, apply the accident
prevention regulations at the installation site and the
technical rules for working with chemicals (e.g.
wearing of protective clothing).
Warning
Before working on the dosing pump and system,
mains cables must be disconnected and secured to
prevent them being switched on again. Before
switching the supply voltage back on, the dosing
lines must be connected such that any chemicals in
the dosing system cannot spray out and put people
at risk.
Warning
Overflowing dosing medium must always be returned
to a tank.
• Media such as peracetic acid and hydrogen
peroxide must be returned to a separate tank.
• Other media can be returned to the dosing tank.
The overflow hose provided with the multi-function
valve must be connected and routed to the
corresponding tank or the cap of the suction lance or
foot valve.
Warning
When changing chemicals, check the chemical
resistance of the materials used. If there is a risk of a
chemical reaction between the chemicals, clean the
DTS dosing tank station thoroughly before dosing the
new chemical.
The installation material for the dosing pump
(screws, nuts, washers) is delivered with DTS dosing
tank stations that have the "Preparation for dosing
pump" option.
Route hoses free from mechanical tension and
bends.
Only use the clamp rings and hose connectors
intended for the hose diameter in question.
Only use original hoses with the required dimensions
and wall thickness.
Observe the maximum permissible operating
pressure.