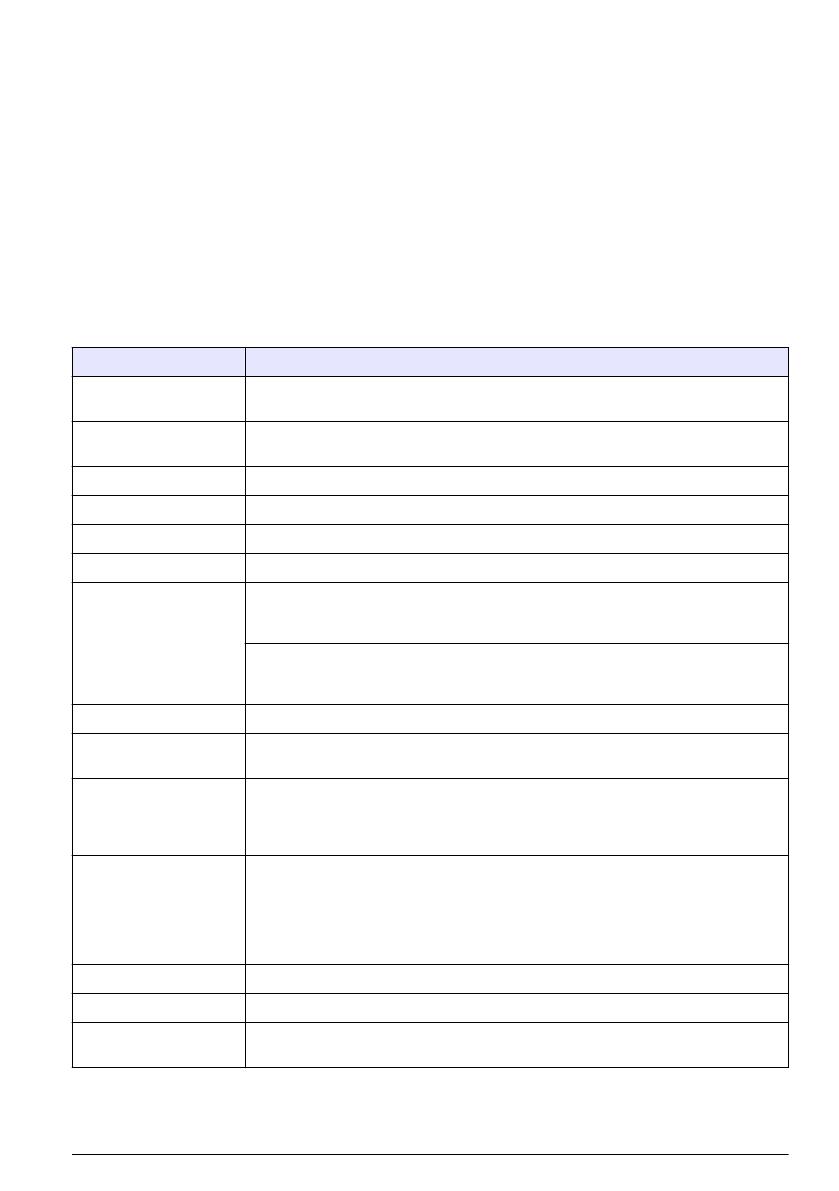
Table of Contents
1 Expanded manual version on page 3
2 Specifications on page 3
3 General information on page 4
4 Installation on page 7
5 User interface and navigation on page 20
6 System startup on page 22
7 Maintenance on page 24
8 Troubleshooting on page 24
Section 1 Expanded manual version
For additional information, refer to the expanded version of this manual, which is available on the
manufacturer's website.
Section 2 Specifications
Specifications are subject to change without notice.
Specification Details
Component description Microprocessor-controlled and menu-driven controller that operates the sensor and
displays measured values.
Operating temperature -20 to 60 ºC (-4 to 140 ºF); 95% relative humidity, non-condensing with sensor load
<7 W; -20 to 50 ºC (-4 to 104 ºF) with sensor load <28 W
Storage temperature -20 to 70 ºC (-4 to 158 ºF); 95% relative humidity, non-condensing
Enclosure NEMA 4X/IP66 metal enclosure with a corrosion-resistant finish
European standards EN 61326-1: 2006; EN 61010-1:2010
ETL approved File 65454
Power requirements AC powered controller: 100-240 VAC ±10%, 50/60 Hz; Power 50 VA with 7 W
sensor/network module load, 100 VA with 28 W sensor/network module load
(optional Modbus RS232/RS485 or Profibus DPV1 network connection).
24 VDC powered controller: 24 VDC—15%, + 20%; Power 15 W with 7 W
sensor/network module load, 40 W with 28 W sensor/network module load (optional
Modbus RS232/RS485 or Profibus DPV1 network connection).
Altitude requirements Standard 2000 m (6562 ft) ASL (Above Sea Level)
Pollution degree /
Installation category
Pollution Degree 2; Installation Category II
Outputs Two analog (0-20 mA or 4-20 mA) outputs. Each analog output can be set to
0-20 mA or 4-20 mA, and can be assigned to represent a measured parameter such
as pH, temperature, flow or calculated values. Optional 3 additional analog outputs.
Secure Digital Memory card for use in data logging and software updates.
Relays Four SPDT, user-configured contacts, rated 5A 250 VAC (resistive). Contacts are
rated 250 VAC, 5 Amp resistive maximum for the AC powered controller and 24 VDC,
5A resistive maximum for the DC powered controller. Relays are designed for
connection to AC Mains circuits (i.e., whenever the controller is operated with 115 -
240 VAC power) or DC circuits (i.e., whenever the controller is operated with 24 VDC
power).
Dimensions ½ DIN—144 x 144 x 180.9 mm (5.7 x 5.7 x 7.12 in.)
Weight 1.7 kg (3.75 lb)
Digital communication Optional Modbus RS485/RS232 or Profibus DPV1 network connection for data
transmission
English 3