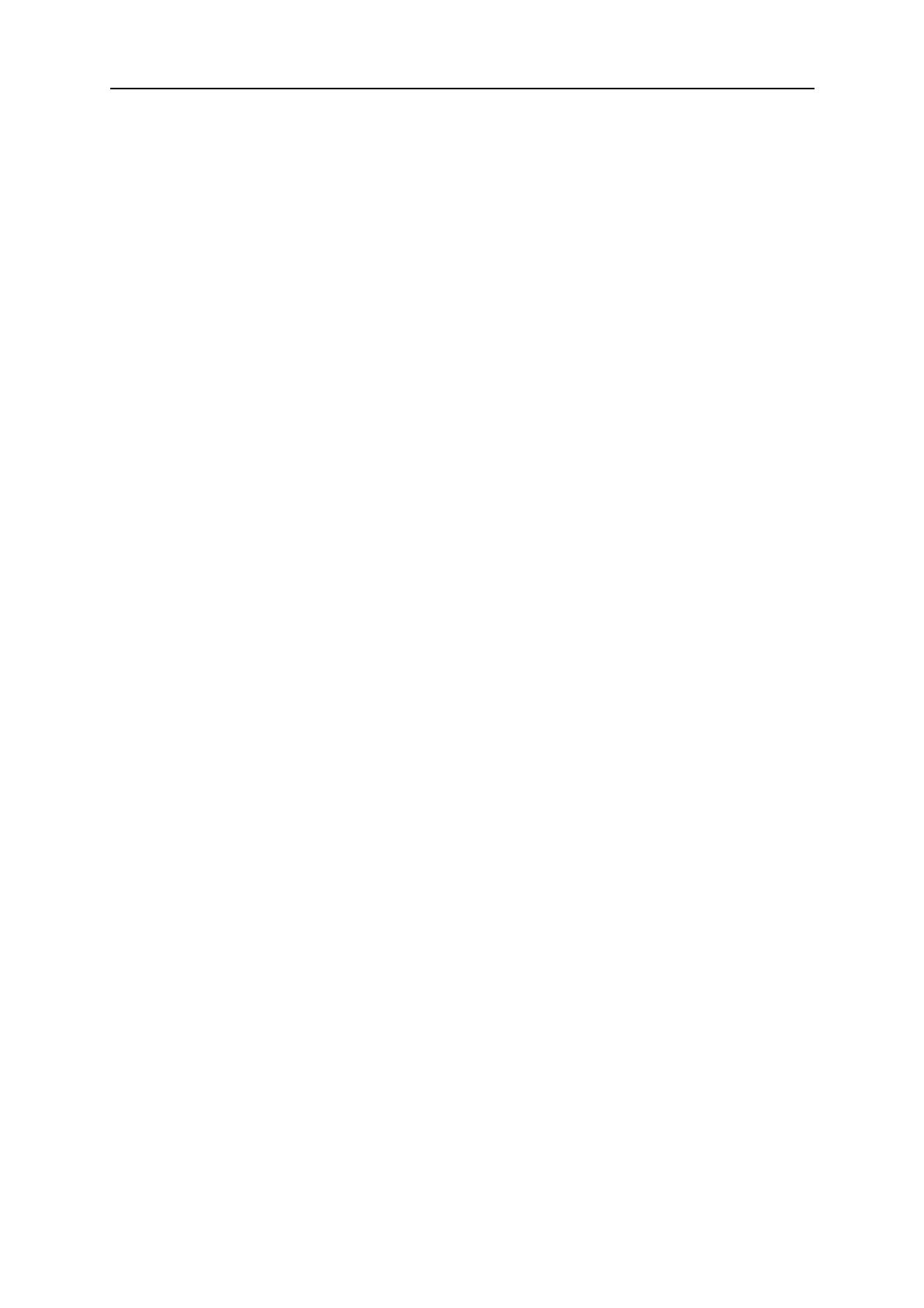
TABLE OF CONTENTS
0463 341 131 © ESAB AB 2013
1 WARNINGS........................................................................................................... 4
2 SAFETY ................................................................................................................ 5
3 INTRODUCTION................................................................................................... 8
3.1 Overview ............................................................................................................... 8
3.2 Equipment.............................................................................................................8
4 TECHNICAL DATA ............................................................................................... 9
5 INSTALLATION................................................................................................... 11
5.1 General................................................................................................................ 11
5.2 Lifting instructions............................................................................................. 11
5.3 Location .............................................................................................................. 11
5.4 Mains supply ...................................................................................................... 12
6 OPERATION ....................................................................................................... 14
6.1 Overview ............................................................................................................. 14
6.2 Connections and control devices.....................................................................14
6.3 Connecting welding and return cables ............................................................15
6.4 Turning the mains power on/off........................................................................15
6.5 Fan control..........................................................................................................15
6.6 Symbols and functions......................................................................................15
7 MAINTENANCE.................................................................................................. 18
7.1 Overview ............................................................................................................. 18
7.2 Power source......................................................................................................18
7.3 Welding torch .....................................................................................................18
8 TROUBLESHOOTING........................................................................................ 19
9 ORDERING SPARE PARTS ............................................................................... 20
DIAGRAM ..................................................................................................................78
ORDERING NUMBERS.............................................................................................79
ACCESSORIES .........................................................................................................80
Rights reserved to alter specifications without notice.