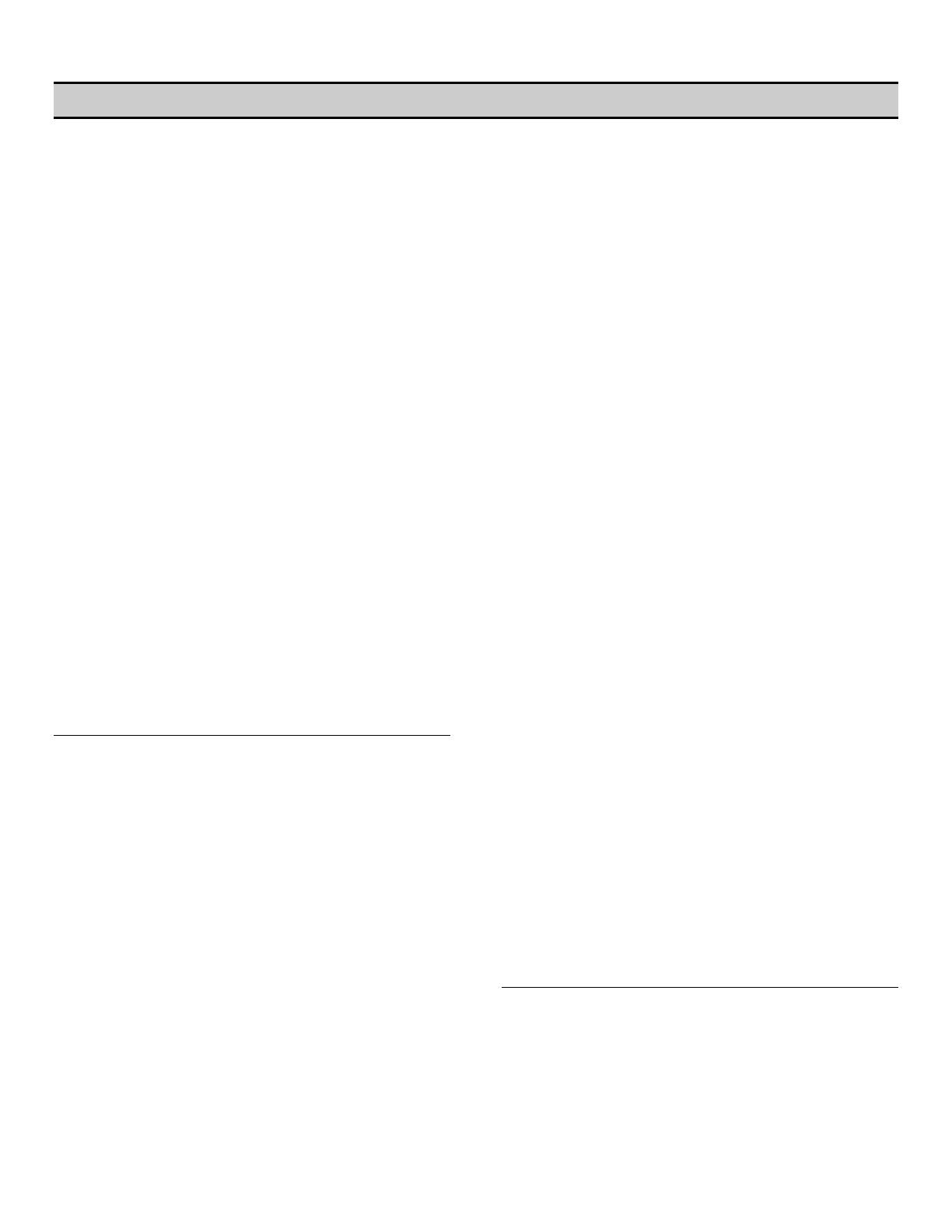
5
SECTION 5 — BEFORE YOU START
Prior to attempting installation and commissioning of the
X4I please review the following check list:
o Quick Set Up Manual is available and has been
reviewed
o Application Guide is available and the correct
diagrams have been identified
o If the specific diagrams are not in the Application
Guide the specific compressor control wiring
schematic will be required to define the correct
interconnection
o Operator’s Manual is available and has been
reviewed
o Compressors to be connected can accept remote
load / unload commands
o Compressors to be connected have automatic
Start / Stop capability
o Correct compressor controller EPROM is installed
or available to allow Remote Control and Auto
Start/Stop (SE Controller)
o The correct wire is available to connect the X4I
with the Compressor / IR-PCB interface
o The correct wire is available to connect the X4I
with the pressure sensor/transducer
o The X4I can be located within 330ft (100m) of
each compressor
o The Pressure sensor/transducer can be located
appropriately within 330ft (100m) for the X4I
Controller
CHECK LIST GUIDANCE
o Electrical Drawing For Each Compressor: It is
important to have the Electrical drawing for each
compressor so that the correct interconnect
drawing can be referenced from the Interconnect
and Application Guide
o Types of Compressors To Be Sequenced: Refer
to the Interconnect and Application Guide for
specific details on the types of compressors that
can be sequenced and their individual
requirements such as Auto Restart, Intellisys
Software, etc.
o IR-PCB Mounting: The IR-PCB module is
designed to be installed within the compressor
starter enclosure. The mounting location of the
IR-PCB should be away from any high voltage
connections, contactors, or transformers.
o IR-PCB and Compressor Interconnections: Refer
to the Interconnect and Application Guide for
specific drawings for various compressors and
the X4I. If there is not a specific drawing
available for the compressor being sequenced at
the site, please contact Technical Support
Services for assistance.
o IR-PCB and Compressor Interconnection Wire:
The X4I is supplied with 100 Ft (100m) of 18
gauge stranded wire (Orange) to use for the
connections between the IR-PCB and the
compressor. In most cases, this is sufficient for
most installations. If additional wire is required,
any 18 gauge stranded wire can be used in lieu
of the wire provided in the kit.
o X4I and Compressor Interconnect Wire: The X4I
and the compressor IR-PCB interconnection is
designed to use 7-conductor shielded cable or
individual wires run through earthed/grounded
metal conduit/tubing. (18 gauge wire)
o X4I and Pressure Transducer Wire: The X4I and
the pressure transducer interconnection is
designed to use 2-conductor shielded cable.
(18gauge)
o All external wiring to the X4I should be made
through the holes (grommets) provided in the
X4I enclosure (8 in total). Drilling or tapping
additional holes in the enclosure can result metal
shavings making contact with the circuit boards.
Damage due to metal shavings in the circuit
boards is not covered by warranty.
o Power / Local Disconnect (Breaker): Incoming
power (115VAC/230VAC, single phase) should
be fused (50VA) and a local disconnect provided.
The power source should be regulated and noise
free. The use of a power supply regulator might
be required in applications where unregulated
power is an issue
o Confirm that all electrical connections are made
properly and tightened and conform to local
standards.
o Common Receiver: The X4I must have its
pressure transducer located in a common
receiver for proper Wet Side or Dry Side System
pressure control.
o Pressure Transducer Installation: The pressure
transducer threads are BPT. It is the equivalent
of ¼” NPT.
ASSISTANCE
o Contacting Technical Support Services or Service
Bulletins listed on the IR ServiceNet can provide
further assistance if there are other questions or
concerns prior to Installation and Start-up.
o